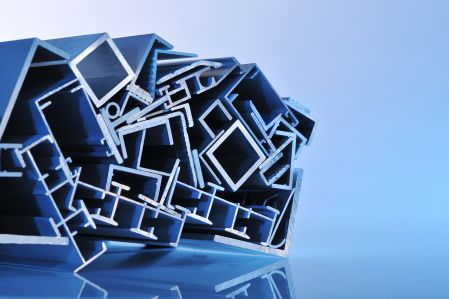
Aluminum is a versatile material with a wide range of applications. But where does aluminum actually come from? And how is aluminium produced? Read all about the origin and the aluminium production process in this blog!
The beginning: bauxite
Aluminium is extracted from bauxite. Bauxite is the name for the ore in which around 30 to 54% of the aluminium oxide is contained. Because of the fact that aluminium has a tendency to bind with oxygen, there is very little pure aluminium found naturally. Aluminium is only available in the form on an oxide, i.e. metal bound with oxygen. This aluminium oxide has to be extracted from the aforementioned bauxite.
Bauxite is primarily extracted in (sub) tropical areas because this bauxite contains the highest quantities of alumina. Alumina is the name for pure aluminium oxide. The extraction of alumina from the bauxite usually takes place in the vicinity of the bauxite extraction site to save on transport costs.
Extract alumina from the bauxite
The alumina is extracted from the bauxite by means of the so-called Bayer process, named after the inventor of the process Karl Bayer (in 1887). A large quantity of bauxite is finely milled. This bauxite is then poured into a large container to which heated caustic soda is gradually added. Caustic soda is a solution of corrosive soda and water. The caustic soda dissolves the aluminium oxide that is found in the bauxite. The other elements of the bauxite do not dissolve.
The liquid mixture of caustic soda and the dissolved aluminium is referred to as ‘slurry’. The remaining substance from the bauxite is called ‘red mud’. The slurry is separated from the red mud via filters. Red mud is disposed of as waste. The slurry is then cooled and transferred to precipitation tanks, also called precipitators. Small white crystals then form in the liquid and fall to the bottom. From there, they are pumped to another tank where the crystals can continue to grow.
The crystals are then taken to an oven where they are converted to alumina at a temperature of 1000℃. This alumina looks like a fine white powder and can be further processed to obtain pure aluminium.
Electrolysis process creates pure aluminum
The alumina is transported to the primary smelters, or aluminium factories. They are often located where cheap and relatively clean energy can be generated. These primary smelters turn the alumina into pure aluminium using the so-called Hall-Héroult process. Alumina comprises aluminium and oxygen and the aim of this process is to separate the two.
The alumina is poured into a reductive container. This container is filled with the fluoride salt cryolite, which is then heated to a temperature of 1000℃. The interior of the container is covered with graphite. There are also two carbon anode-blocks hanging in the container.
Between the anode-blocks and the graphite, an electrical charge is generated with the low voltage (4-5 Volt), but a massive amperage of 220,000-340,000 Ampère. This electric current separates the oxygen from the aluminium. The oxygen binds to the carbon on the anode-blocks and is removed in the form of CO2. The pure aluminium sinks to the bottom where the liquid is drained off. The liquid aluminium is then poured into forms so that it can be further processed for a range of applications.
The complete extraction and production process from aluminium
The complete extraction and production process from aluminium is a fascinating procedure. Would you like to know more about this entire process, with additional issues such as the energy requirements of the production and waste substances that are released? Read more about it on our website: